The many facets of the plastics industry
The plastics industry produces for very heterogeneous markets, with different target groups and requirements. These must also be taken into account when choosing the lubricants. Plastic parts for the technology industry require high levels of precision, those for the food industry or toys must be harmless. This applies to small and large plastic parts, for small runs and mass productions.
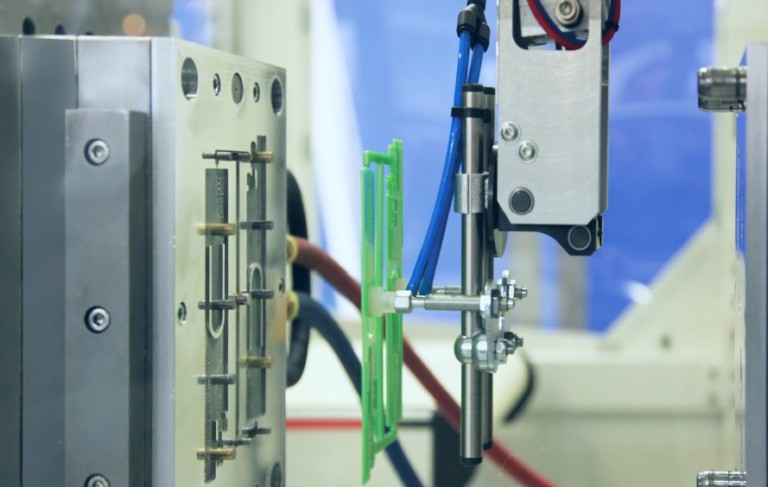
Challenges in plastic injection molding production
In the production process of the plastic injection molding industry, impeccable quality and maximum production efficiency are decisive success factors. Different processes are used to bring plastics into the desired shape. The machines and systems used are exposed to extreme loads.
Enormous forces of several hundred kilonewtons and temperatures of over 200 ° C are at work. In order for the machines and systems to produce reliably over several years, special lubricants are required that are precisely tailored to the tribological requirements of the individual lubrication points.
Tribological solutions for the lubrication of the injection molding machine
As a manufacturer, TUNAP provides a professional range of release agents and lubricants, cleaners and products for surface protection, with which, for example, the highest possible number of shots can be achieved in the plastic injection molding industry.
Higher production efficiency
Investing in high-quality lubricants makes up a comparatively small part of the maintenance budget of a plastic injection molding system. However, these lubricants can significantly increase the productivity of the entire plastic injection molding system.
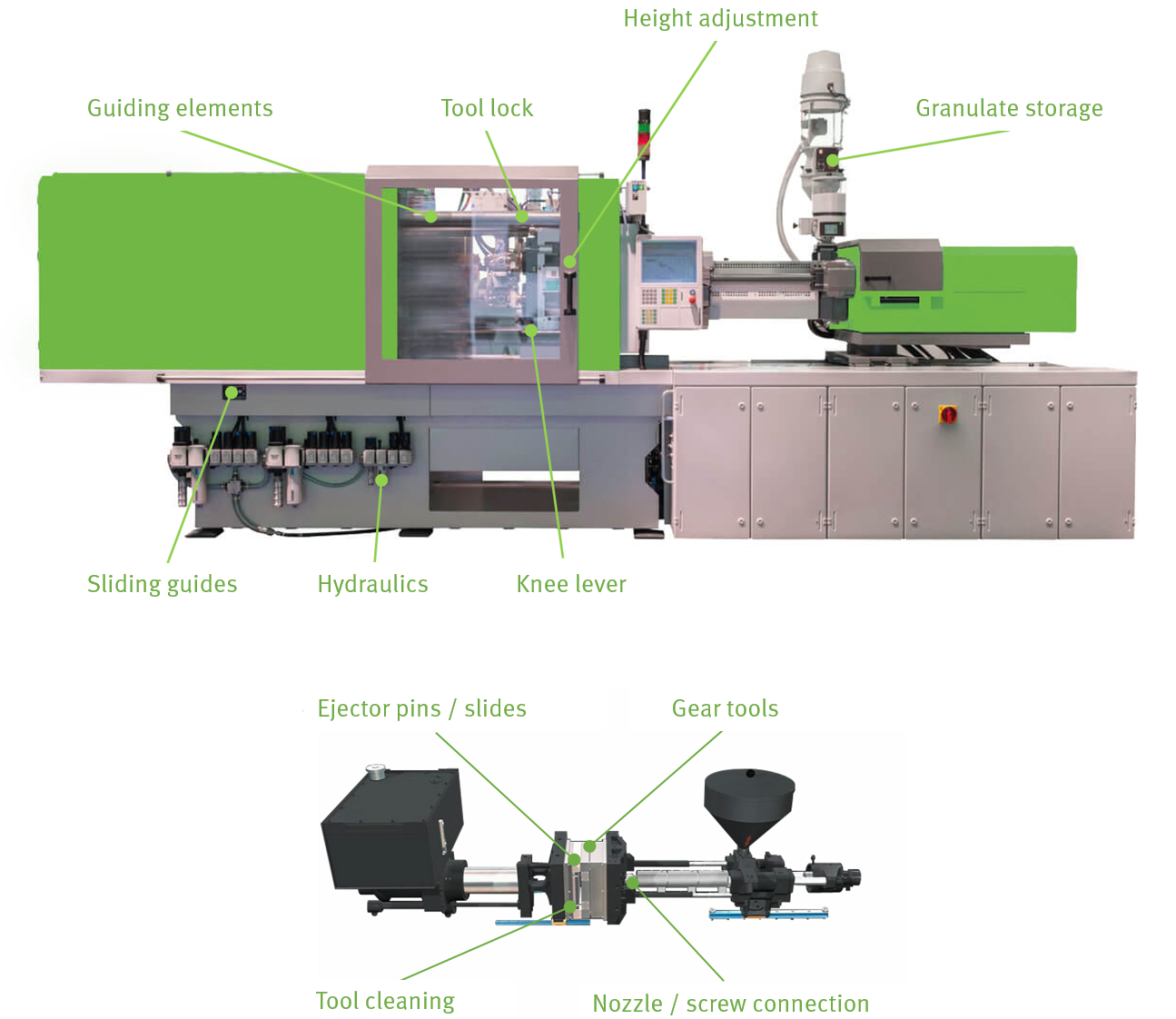

The all-rounder: TUNGREASE CP-2/200
The fully synthetic TUNGREASE CP-2/200 deserves special mention as a universally applicable lubricating grease.
Wherever high loads occur, for example in toggle levers, on sliding guides or on guide elements, the extremely good surface protection comes into play and ensures that the components have a longer service life.
In addition, the consumption of lubricant is reduced, as the long-term effect enables longer relubrication intervals.
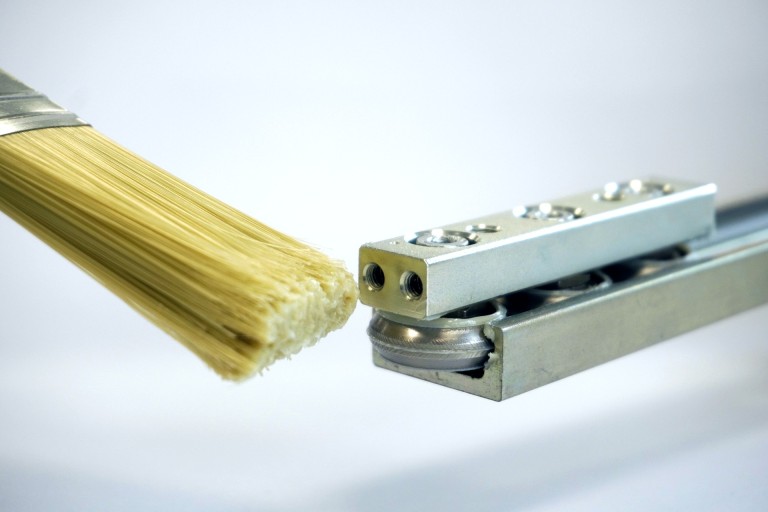
The classic: TUNGREASE SG
TUNGREASE SG is the classic in our portfolio for plastic injection molding. The ingredients are extremely high quality and it is highly pure. A small amount of TUNGREASE SG is sufficient to reliably lubricate the precise tolerances in ejector pins and slides without being stripped off.
Injection molded parts are not soiled or contaminated. In addition, it is extremely temperature and evaporation stable, compatible with all plastics and very excellent long-term lubricating effect.
Prioritization of lubrication
Injection molding systems in the plastics industry are expected to perform at their best under extreme pressure, fluctuating temperatures and under the most adverse conditions. With such requirements on lubricants, product formulations with highly optimized protective and stability properties are the first choice. The prioritization of lubrication as part of a systematic maintenance strategy lowers the total operating costs, for example through shorter start-up times, lower energy consumption and optimized cycle times.
Certificates and NSF
With ISO 21469, TUNAP has been proven to meet the most comprehensive hygiene requirements in the production of H1 lubricants. The international certification is the most demanding proof of safety, reliability and product responsibility. The standard requires a holistic view of the life cycle of an NSF H1 product. The strict regulation of the recipe, ingredients, production, handling, packaging, storage and use ensures the highest quality.
Contact Us
Do you have any questions about lubricants for the food industry or are you looking to contact our experts? We are happy to help.