Lubricants for the Food and Beverage Industry
As a lubricant expert for the food, beverage and feed industry, TUNAP offers you high-performance specialty lubricants with NSF-H1 registration.
Our high-performance, food-grade portfolio of release agents, lubricants, cleaners and surface protection products was specially developed for the food and beverage industry. In addition to the technical requirements, our focus is on hygiene, product safety and certification.
H1 Lubricants and Where They are Used
H1 lubricants are food grade lubricants. They are used where there is occasional or technically unavoidable contact between the lubricant and food products.
The requirements for lubricants for the food and beverage industry are as varied as the food itself. Production is sometimes carried out at extremely high temperatures of over 200° C or extremely low temperatures of down to -40° C. In order to protect metal or plastic surfaces, the lubricants used must, in addition to temperature resistance, often be adhesive, acid and alkali-resistant as well as resistant to water and surfactants.
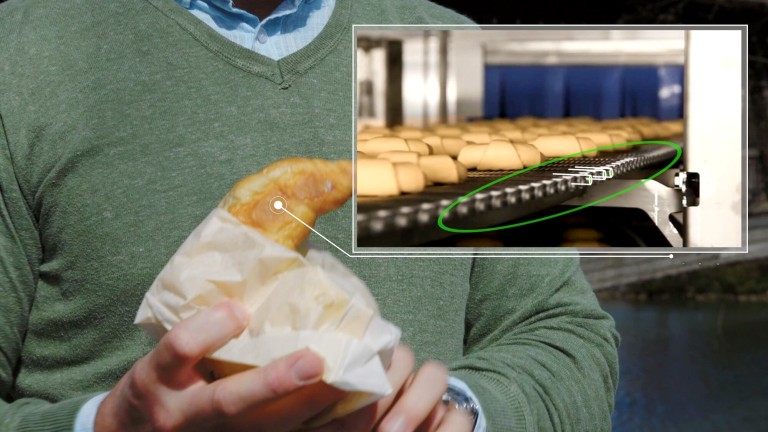
Use of H1 lubricants for conveyor belts in food production.
Food Safety for Consumers
Since lubricants in the food and beverage industry can come into contact with food products, they must be food-compatible and particularly safe for consumers. They need to
- comply with food law regulations,
- be physiologically perfect,
- be odorless, colorless and tasteless and
- they must not offer any habitat to microorganisms.
Food Grade and Certifications of our Lubricants
TUNAP products used in the food and beverage industry meet the requirements of
- Kosher (suitable, pure) according to Jewish dietary laws) and
- Halāl (marking for products that are halāl (permitted) under Islamic law).
In addition, our products are registered by the NSF (National Sanitation Foundation). The NSF is a US authority for testing the food compatibility of lubricants. As a lubricant manufacturer, we are obliged to submit all components of our H1 lubricant formulations to the NSF for testing. The relevant NSF certified lubricants in food quality can be found on the website nsfwhitebook.org.
With the internationally recognized ISO 21469 standard for the food industry, TUNAP meets the strictest hygiene requirements for H1 lubricants and the entire production process, including manufacture, handling, packaging and storage.
The Food and Drug Administration (FDA), also based in the US, maintains a list of base oils and additives that may occasionally come into direct contact with food in low concentrations. The FDA has set 10 mg of lubricant per kilogram of food as a limit value. This amount also prevents contamination by MOSH / MOAH due to the lubricant used.
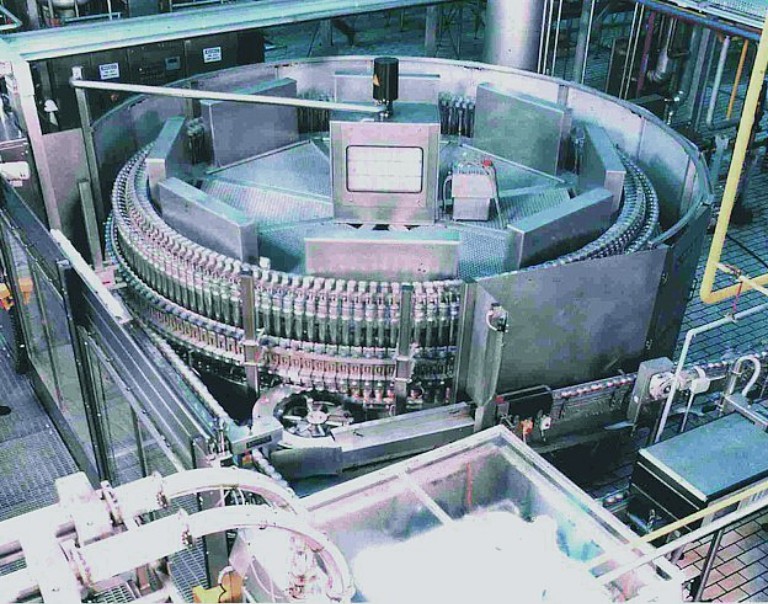
H1 lubricants in bottling.
Technical Requirements for H1 Lubricants
In addition to the requirements for hygiene, product safety and certification, there are special requirements in the food industry with regard to the lubrication of
- plants.
- conveyor belts,
- roller and plain bearings,
- transmissions,
- oil circulation systems,
- chains,
- mixers,
- pumps,
- tanks and
- pipelines
to name a few.
As Efficient as Conventional Lubricants
Machines that are used in food processing companies face challenges in terms of tribology and lubrication that are comparable to those of non-food processing companies. H1 lubricants must be just as efficient as conventional lubricants and develop their full effect even under extreme conditions in food processing. You need to
- ensure similar protection of the inner surfaces to control friction, wear, corrosion, heat and deposits,
- offer good pumpability, oxidation stability, hydrolysis stability and thermal stability in various areas of application and
- in contact with food, certain process chemicals, water and bacteria - especially in the area of food and drug production - do not show any loss of performance.
Advantages of our H1 lubricant solutions
By using our H1 lubricants, you increase food safety for consumers and you benefit from lower downtimes and maintenance intervals for your systems and machines - which in turn saves you time and money.
H1 Lubricants: Mineral or Synthetic Base
H1 registered lubricant base materials can be either mineral or synthetic:
- Petroleum based lubricants: Mineral oils used in H1 food grade lubricants are either technical grade white mineral oils or USP grade white mineral oils. They are highly refined, colorless, tasteless, odorless and non-staining. USP mineral oils are the most highly refined of all white mineral oils.
- Synthetic lubricants: Synthetic H1 lubricant bases are often polyalphaolefins (PAO). Compared to white mineral oils, they have a significantly higher oxidation stability and a wider range of operating temperatures. Other approved synthetic H1 base oils are ester oils, polyalkylene glycols (PAG), dimethylpolysiloxane (silicone) and perfluoropolyether (PFPE). Compared to the first-mentioned base oils, silicones and perflour polyethers have an even higher temperature and oxidation stability.
Contact Us
Do you have any questions about lubricants for the food industry or are you looking to contact our experts? We are happy to help.